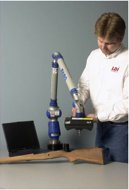
It was about 20 years ago when the first non-contact scanning devices became readily available. Their acceptance was surprisingly slow given that they had the potential to dramatically cut down the time it took to capture geometry for reverse engineering.
3D Scanners – Evolution in Design and Development
Arm-Based 3D Laser Scanner
In the mid 1990s the more advanced design and development companies had adopted 3D solid modeling software at the center of their product development process.
In order to fully enjoy the benefits of working in 3D there was a need to be able to model every aspect of a new design. The problem was that design might include many actual existing parts for which there was no electronic data available.
Examples of this were:
- Legacy parts designed in 2D
- Parts made by suppliers for which no CAD was available
- Human bodies
- Other organic shapes needed for design simulation or visualization
In response to this vital need, a number of new technologies emerged. One notable technology was the line laser scanner mounted on a CMM or Portable Arm such as those from Faro or Laser Design, Inc. Another development at the time were 3D Scanners and Structured Light Scanners, such as those from Steinbichler, GOM and Cognitens.
Despite the tremendous benefits to be had from adopting these technologies their acceptance was surprisingly slow. Partially, this was because of the cost (most solutions with software would cost over $100k.) Another problem was the need to acquire new skills to use the technologies.
But, the biggest reason was many companies simply failed because they did not understand the potentially game changing benefits that made the cost, time and effort justifiable.
3D Scanners – 20 Years Later
Today, the prices of laser, White light and Blue light scanners have come down significantly and the software supporting them has become much more powerful and easier to use.
It may have taken a bit but anyone involved in the design and development process is working in 3D scanning appreciates the benefit of being able to capture 3D geometry. Engineering and design students all use 3D scanning technologies at college and expect to find them out in the workplace.
So, two decades later, the argument of whether 3D scanners are useful in the product design and development process has been fully won and anyone involved is aware of the benefits and their adoption is widespread.
That being said, the number of 3D scanners sold are low in comparison to conventional measuring devices such as Coordinate Measuring Machines (CMMs) simply because there is a limit to the number of 3D Scanners any company needs for reverse engineering, design and development.
Which brings us to another question and new argument taking place now, “Can non-contact 3D scanning take the place of conventional technologies for the inspection and quality control of production parts?”
3D Scanners – What about inspection and quality control?
From the very first appearance of 3D Non contact scanning technologies their makers have put at least as much emphasis on their potential use for inspection and quality control as they have done on reverse engineering and data capture for the development process.
The websites and brochures describing 3D non-contact scanners and 3D scanning technologies suggest their use on the shop floor for production parts measurement is widespread.
In reality, this is not the case.
In fact, there are very few manufacturers that actually use 3D non-contact scanning methods for measuring production parts.
The reasons cited for slow adoption of 3D scanning systems such as laser, blue light and white light scanners for production parts inspection have some similarities of those given for earlier technologies:
- Cost/High Prices
- Time to train in new technology
- Limitations (perceived or real) of current 3D scanning technologies
For example, currently, most 3D scanners are not robust enough for shop floor use and they require highly skilled and trained operators.
There are also two major technical drawbacks in most systems:
- White light and blue light systems can’t measure recently machined or polished metal surfaces unless they are painted or coated so they are not reflective.
- For almost all 3D scanning systems there are no ISO standards applicable to satisfy quality and traceability requirements.
Not all 3D scanners are created equal
3D Optical Scanner – Wenzel CORE
Wenzel CORE Optical Scanner
One system that has overcome these issues is Wenzel’s CORE machine that uses a unique high intensity light spot sensor mounted on a high speed shop floor CMM. This sensor allows it to measure the shiniest of parts with very high accuracy and precision.
In fact, it can measure the thickness of a fingerprint on a mirror.
In addition, it can be calibrated to ISO 10360, opening the door to measurement of safety-critical polished aircraft turbine blades where it is quickly becoming the industry standard for this application.
By overcoming the limitations of the current 3D scanning systems the CORE machine is proving the case for this technology in inspection and quality control.
In the case of turbine blades there is demand for 100% inspection of complex and highly polished parts where those two characteristics rule out the use of CMMs or other optical scanners, the CORE 3D scanner clearly wins the argument of using optical scanners in production measurement.
Surgical implants are another application that is likely to become fertile ground for this technology because there are no other solutions that meet the requirement for accurate, traceable measurement and are also fast enough to prevent quality control being a production bottleneck.
3D scanning and 3D scanners – What is the Future?
Looking ahead, the area of manufacturing that generates the most “buzz” is additive manufacturing or 3D printing. It promises so much, but is facing similar challenges to non-contact 3D measurement.
How do you get out of the development and prototyping lab and into serious production of parts?
Industrial CT Scanner – Wenzel exaCT S
Parts that cannot be made by conventional means probably can’t be measured by conventional means either. So, even if a manufacturer makes the parts with a 3D printer, he can’t measure them. And if he can’t measure them, he can’t sell them to demanding customers in the aerospace or medical industries.
Because of the way that additive manufacturing works, the only sure way to be able to measure the parts made is using a device not limited to line of sight or the need to gain physical access. The perfect solution to this challenge is the CT scanner, used as a metrology tool.
The development and use of industrial CT scanners for metrology almost mirrors the development of additive manufacturing machines. Industrial CT is running a few years behind, as most current CT machines for metrology are generally large, expensive and slow. They are also mostly in the hands of service providers rather than end users.
If 3D printed and additively manufactured parts are to find acceptance in highly regulated fields like Aerospace and Medical, CT machines are going to have to become more widely used for metrology purposes.
At this time and into the foreseeable future, industrial CT is the only game in town for measuring the complex parts that only additive manufacturing can make. Wenzel has developed the exaCT series of desktop-sized CT for this purpose.
3D Scanners – Why quality control & inspection are slow to adopt?
The same basic reason design and development were slow to adopt them 20 years ago.
While there are some minor and apparent reasons manufacturers are slow to adopt new technologies. Things like price, time to learn, and effort involved.
Even some legitimate technology-based questions like – “it can’t measure shiny parts” or “it won’t last on the shop floor.” At Wenzel America, we are answering many of those questions for our customers and winning the technical limitations and other arguments more and more every day.
Ultimately, the basic reason manufacturers are slow to adopt non-contact 3D scanning technologies into inspection, quality control, shop floor and production measurement is a simple lack of understanding of its current and future potential.
It’s exactly the same argument against 3D scanning in design and development 20 years ago, and as an industry — We created new systems, innovated, brought costs down, sold — and thus, won that argument.
We’re doing the same thing today and very soon we will win this one, too.