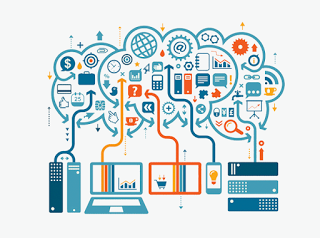
If you spend any time at all online reading business articles, you’ve likely noticed that we are in the midst of a technology shift which is quickly and fundamentally changing our manufacturing world.
We are entering an era of massive amounts of data, being brought together by the growing connectivity of our infrastructure, often referred to as the Internet of Things.
This transition, coupled with increasing automation in the workplace, creates mountains of data which should give us the ability to see into our processes, products, and our companies as whole, transforming how we do business.
But will it really? Will all this data make our collective lightbulbs go off, helping us to manage and improve our processes in the most efficient way possible? That should be the goal of course, but as with any new paradigm, it can be easy to miss the mark.
Take CMM data for example. For over 50 years, there have been CMMs available in Quality labs all over the world, bought with the promise of improving the parts being made. But simply inspecting parts, collecting piles of data, and labeling items good or bad, doesn’t really make the most of the investment that has been made in the tool.
A CMM is most valuable when the data you collect, can drive improvements in your process. The results from inspection should feed decisions in manufacturing to reduce downtime, improve throughput, and efficiency. These things will likely lead to better profits, and customer satisfaction. How do you get there?
With Quality Inspection data the answers are all around us. In the automotive industry AIAG provides resources for building and maintaining a Quality program that uses statistical controls to help you make decisions; in other words, driving your process with your data.
If you make Medical devices, the FDA sets out numerous guidelines not only for Quality, but also relating good manufacturing processes.
Not to be left out, the Aerospace Industry is guided by SAE International and their AS9100 guidelines, providing all manner of guidance from CAD data integrity, to standards for reporting results.
The IoT data available to us now, is a bit different though from the topics above. There isn’t necessarily a white paper or industry standard on how to manage this information and make decisions from it, but that doesn’t mean the old ways don’t work. If we step back and look at it from a broader perspective, data is data. The basic tenets of the guidelines from each organization above, have some very similar structure, regardless of the product or process. The main principles are:
- Understand the key characteristics of your product or process and plan accordingly
- Use an effective tool to monitor these items
- Ensure you monitor with enough frequency that you can trust your data
- Make decisions with the data
- Monitor the outcome
- Adjust as needed
If we take this broad view to the topic, we can then apply this philosophy to any data we now have available throughout our organization. Simple right? The problem is, in this modern era, the data is coming faster than ever before, and is so readily available that we often skip steps in the planning process, assuming that the speed and quantity of data will make careful planning a thing of the past. This strategy however, typically leads to less answers than one started with, and the typical reaction is then to scrap it all because the outcome isn’t what was expected. This is often when you hear things like, “doesn’t work in OUR plant…”.
To avoid this outcome and position your company for success in this new data minefield, the planning portion of the process I outlined above becomes even more critical. Understanding your process; what drives it, the key inputs and variables, and what you want to gain from monitoring, are all of paramount importance.
For example, focus your energy on those items that affect the end product; fit, form, or function. Use accounting or finance data to look for areas of high cost in your process where more monitoring might help you eliminate waste. How does the temperature and humidity in the plant affect your quality? Or the staff?
It’s really no different than checking parts on your CMM. You wouldn’t waste time inspecting features on the part that have no bearing on the performance, or the customer’s quality. In fact you probably take the data you do gather, and look for ways to reduce cost in manufacturing, or reduce inspections on items that aren’t critical; all to save time and money.
When we turn that spotlight on our broader processes, the intent should the same. But the questions we can ask in this connected age are limitless and managing metrics can be a full time job. Driving the charts in an upward trend can easily become an obsession that feels like an end in itself. But the data is only valuable if it drives improvement in your business; making your products and processes, better, faster, and more efficient.
But let’s not forget the skills and techniques that got you to where you are. The basic problem solving principles that you use daily to ensure product compliance, can easily translate in this new paradigm, and can help you drive improvements throughout your organizations.