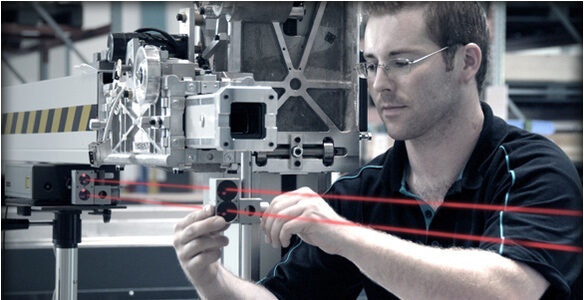
Considering a service provider to certify and calibrate your metrology equipment?
Your quality department has a written policy stating the exact interval of service your CMM needs to adhere to in order to maintain accuracy. Having a service provider do this means you know the performance of your CMM is precisely up to its specifications like ISO 10360,, ASME, or VDI / VDE and you don’t have to have your own people trained in another complex procedure. In some cases 3rd party service providers are equal to CMM manufacturers’ service departments, in other cases, maybe not.
What do CMM certification and calibration entail?
All CMM service providers compare the errors of your Coordinated Measuring Machines against known standards. In the case of CMM Certifications, any errors will only be verified and reported to you. In the case of a full CMM Calibration, they are verified and corrected. Depending on the service provider you choose, their capabilities and certification levels will vary. The minimum accreditation you should look for is the industry standard – ISO/IEC 17025. The article, Calibration vs. Certification from Quality magazine covers the definitions in detail.
When should CMM Calibration be done vs. CMM Certification?
The frequency of service of CMM calibration or CMM certification depends on what your quality program requires. Typically, the rule of thumb given by most manufacturers calls for a full CMM calibration every 2000 hours. This works out to about once a year based on an estimated usage of one eight-hour shift per workday. Eight hours per day X 5 days per week = 40 hours a week. 50 weeks X 40 hours = 2000hrs.
Who should do the calibration and certification of your CMMs?
That depends.
If you just need to verify potential machine errors against a known standard, this could be done with equipment like an MCG (Machine Checking Gauge) system for CMM performance monitoring. You could get your own system and train your own people. This gives you the ability to easily verify your CMM is okay after a collision or in between your regularly scheduled service intervals. This level of testing can be done in as little as 10 minutes in many cases and gives you interim verification of volumetric accuracy to ISO 10360-2 standards.
It will also definitively show you when you need to have 3rd party or factory calibration services and could save you money and downtime as a result. So, in many cases an MCG could be a good investment, even when you’re on a regular measuring machine maintenance and calibration plan.
Do you require full calibration to ISO 10360 standards?
If your quality system requires full calibration with any errors found also corrected, how that is done depends on the company performing your CMM calibration. They may use measuring gage blocks or a ballbar. Additionally, because calibration also includes correcting the errors, in some cases this may require adjustment of the CAA (Computer Aided Accuracy) or error map. In some cases it may require mechanically correcting errors and even re-lasering the error map for complete correction.
Depending on what the calibration entails, this may not be something a typical 3rd party CMM service provider can do, as they may not have enough experience with the internal workings of certain CMMs or adequate programming knowledge of your software. In these cases getting the service performed by the manufacturer is the best course of action.
Is your CMM service partner familiar with your machine & software?
On the other hand, if they regularly retrofit your specific measuring machine model type and sensors or program the metrology software you use, they may be just as capable as the manufacturer. In any case, using an accredited service is usually much easier and more cost-effective than obtaining the training, equipment and certifications needed to do it in-house. But you have to do your homework.
Obviously, as users of the measuring equipment, you want the machine to have the highest accuracy, maximum availability, and most economical lifecycle-cost possible.
Poor calibration & certification could mean shipping bad parts
Shipping bad parts or producing scrap is directly impacted by the quality department and can cost much more than ensuring your quality system and processes are at their highest standards. Catching bad parts before shipment and giving feedback to the manufacturing processes are a couple of reasons to implement stringent quality standards that include regular metrology calibrations and certifications.
Servicing your CMM in a perfect world vs. reality
In a perfect world you would, of course, have your CMM serviced exactly on the established interval your quality department dictates and you would have the most complete preventative maintenance procedures done in the shortest amount of time possible. This would, in theory, give you perfectly measured parts and 100% uptime. The reality is a bit different.
It looks more like this – create a workable CMM service interval that meets quality requirements, guarantees accuracy creates as little downtime as possible, and stays within budgetary constraints. So, how do you do that?
Choosing the right CMM Certification and Calibration service provider
The answer then is a strategy where you partner with a fully-accredited and experienced service provider equipped to perform calibrations with the least amount of downtime while identifying an intelligent PMs (preventive maintenance) that will keep your CMMs accurate and maximize your uptime. Your service partner needs to hold the certifications that are dictated by your quality department. If you need them to be an ISO 17025 accredited company and have the ability to perform complete ISO 10360 calibration, this gives you a specific pool of available service providers.
9 Questions you need to ask when choosing your best CMM servicing partner
Does the CMM service provider have expertise in the following:
1. Can they mechanically make adjustments to the machine if necessary?
2. Are they able to adjust the error map of the measuring machine?
3. Are they able to use the laser system to remap the CMM when required?
4. Are they aware of the various service notices for your machine types?
5. Do they have the necessary tools to perform the calibration?
6. Do they have access to the latest firmware updates for the controller?
7. Do the technicians have access to factory training for the CMMs?
8. Does the service provider have experience with a variety of CMM types and manufacturers?
9. Do they have technicians who can do calibration and certification on site?
Is Wenzel America the best choice as your Coordinate Measuring Machine Service Partner?
There is a good chance our technicians can perform any calibration needed on any CMM you own, no matter what make or manufacturer or software you use.
We not only sell and service Wenzel CMMs, but, because of our legacy in upgrading used CMMs and recycling good granite with new software and sensors, we have unique experience and flexibility with other company’s CMMs as well. We’re pretty confident you’ll discover we may be the best choice for your CMM calibration and certification partner no matter your specific needs.
And if you want to set up in-house verification we also have the best prices on Renishaw MCG systems. Just fill out this quick form and we’ll get back with you within one business day.
Questions about CMM Calibration and maintenance services? Send us an email at sales.service@wenzelamerica.com or call our service department @ 248-296-4300.