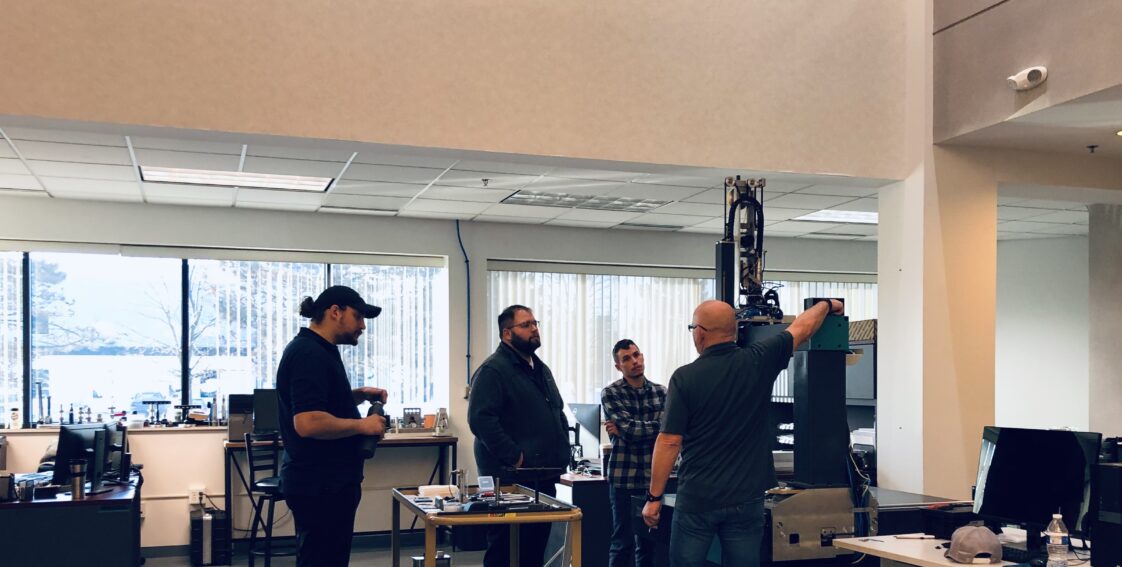
Downtime, uptime and me time… are you ever left feeling like you just don’t have enough TIME?
Between kids, family, work, activities, friends, house projects, work, hobbies, work… and probably more work, we seem to very rarely get the chance to kick back and settle into a little ‘me time’.
We are often measured on our productivity, or what we can fit into a day. In the same way, when we evaluate our manufacturing equipment, we often use the requirement of uptime and availability as a standard to differentiate products and ensure that productivity is maintained.
What to consider during machine downtime.
The two most significant factors when considering machine downtime are scheduled maintenance tasks and emergency repairs. While maintaining your annual calibrations and scheduling them far enough in advance to keep the equipment ‘in spec’ is important, it is clear which of these has a bigger impact on machine availability – the dreaded emergency service.
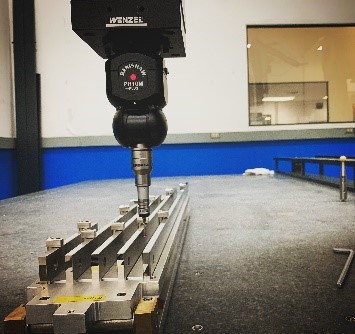
THE DREADED EMERGENCY SERVICE
PC/electronics failures, and other unforeseen circumstances that leave us throwing our hands up in the air but ultimately unable to do anything more than call hotline support for help. The more frustrating examples of downtime are often preventable with a little TLC and preventative maintenance of your machine.
Maintain maximum uptime thanks to planned downtime.
Previously I’ve written about how your CMM is a finely tuned instrument, crucial for quality control. As inspection moves closer to the shop floor, the line between heavy machinery and precise instrument is blurred easily.
While your cutting tools thrive in a coolant and oil filled environment doing the dirty work, when you’re measuring in single digit microns, the biggest enemy of accuracy and uptime can be dirt on air-bearing guideways and dirty air.
Even in an inspection lab, the hustle and bustle of work, preparing parts for inspection, and general dirt build up, is something to be mindful of while striving to maintain maximum uptime of your equipment – expecting your air bearing to push past piles of dirt and grime while the machine attempts to position itself with extreme accuracy, is a recipe for disaster!
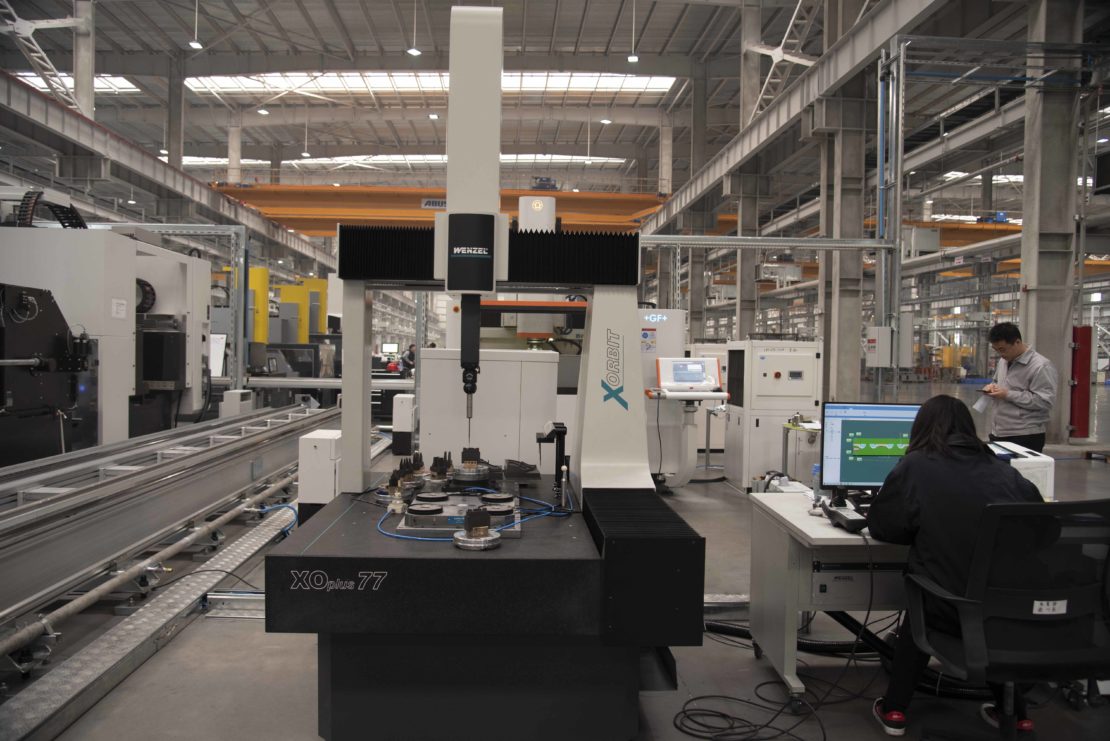
HOW TO ELIMINATE DOWNTIME
So, the next time you’re discussing with your team how to eliminate downtime and measure more parts faster, consider giving your CMM a little ‘me time’. A day at the spa with an isopropyl alcohol bath for the granite guideways. Or perhaps use the WENZEL Stylus cleaner for your over-used probes. Maybe replace the filters in your air system. Simple preventative maintenance tasks like these are great for keeping your CMM clean and free of water, dirt and oil ensuring it stays productive and operational when you need it the most.
Scheduling preventative maintenance tasks for your CMM
If you want to talk about PM tasks for your CMM, don’t hesitate to reach out to me, or any of the WENZEL team. Our job is to help you keep your equipment running smoothly for decades to come! But don’t forget, if giving your CMM a spa day still sounds like too much work to fit into an already busy schedule – come talk to us about our variety of equipment options that come Shop Floor hardened and ready to do battle with the dirt, oil, and temperatures your CNCs adore.
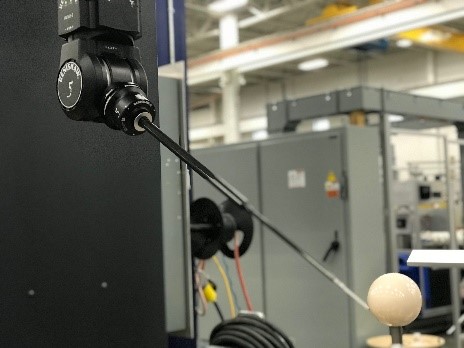
Author
Stuart Nichols is the West and East coast Sales Manager who have been with WENZEL over 6 years with extensive knowledge of WENZEL machines and how to increase productivity for your business through metrology systems. Don’t hesitate to contact him at snichols@wenzelamerica.com or give him a call at (248) 820 7227. You could also follow us on LinkedIn for the latest product information!