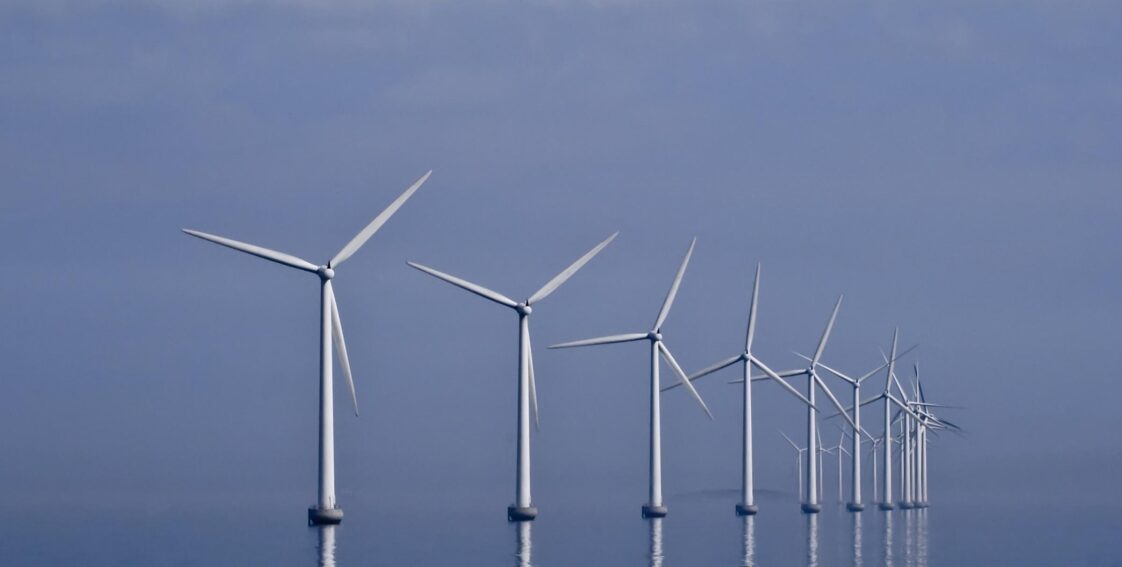
Creating more efficient, sustainable energy sources is vital to reducing the use of fossil fuels as the primary source of power generation. Making Wind Power generators more reliable and efficient is dependent on manufacturing and refurbishing the giant gears and gear boxes that convert the wind into energy.
Power generators built for Wind Power applications have very tight tolerances for dimension, shape and position of movable components. These tolerances need to be precisely followed for the wind turbines to generate efficient power and for the life of the turbines and gearboxes inside them.
Wind Turbine Gears get exposed to heavy environmental changes from temperature fluctuation and high wind speed to foreign object damage and corrosion. Refurbishing and refinishing wind turbine gearboxes can cost more than $300,000 after just a few years in service.
CMM Coordinate Measuring Machines Are Used in Gear Manufacture and Refurbishing
So, ensuring the gears maintain tolerances and are properly maintained is vital to sustainable energy production and wind power generation. When gears are inspected before refurbishing and during original manufacture accurate inspection is done using CMM Coordinate Measuring Machines. Without the knowledge of exactly what damage has been done the gears can’t be refurbished properly. The only way to get this data is with advanced metrology technology and CMMs
Wenzel LHF is a Vital Component is Wind Power Gear Inspection
Wenzel America’s LHF CMM is a highly precise and dynamic CMM with an extremely large measuring range used for Gear Measurement in Wind Power applications. The
LHF CMM also offers excellent access and great mobility. By adding specialized, custom combinations of touch and scanning sensors the highest accuracy is guaranteed.
Our CMM coordinate measuring machines and technology support manufacturers of wind turbine for testing and measuring the critical dimensions of gears necessary for sustainable, green, Earth-Friendly energy production worldwide. (Updated 31JUL17)