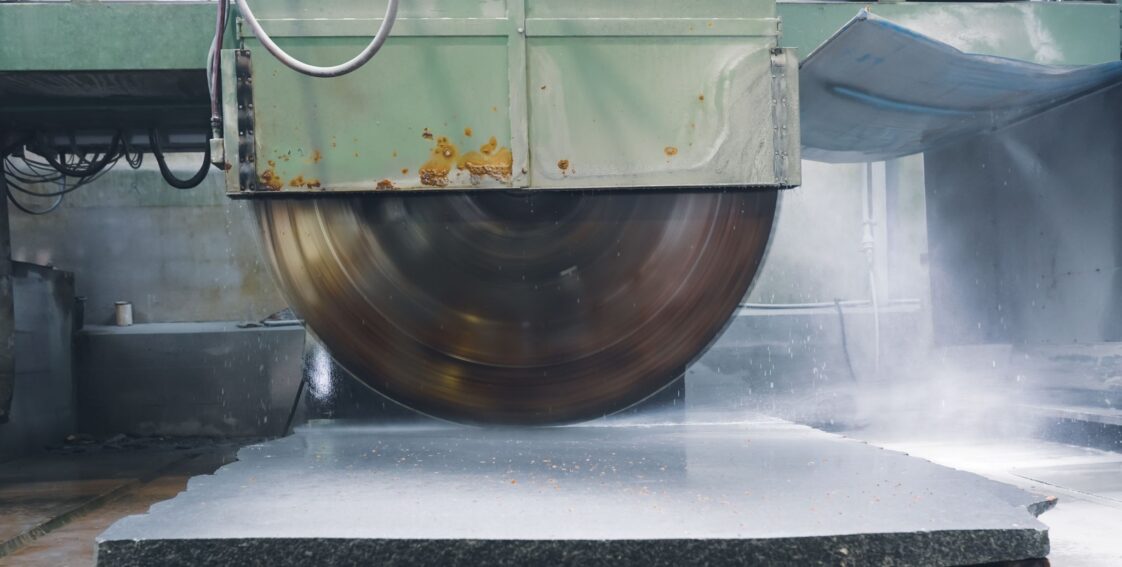
In 1885 in the German village of Gross Bieberau, a stone cutter began a business making tools, utensils, and decorative pieces from the stone of local quarries. He likely never imagined that 130 years later his family would still be cutting stone on the same spot, though for drastically different purposes. Today, Wenzel Steintechnik stands on the same ground, run by the same family as it has since 1885, making the granite bases and components for Wenzel CMMs.
A division of Wenzel Gmbh since 2006, Steintechnik evolved over the years from simple hand carved items, to designing and fabricating tombstones, evolving to the production of granite for industrial applications, and along the way became a critical partner for Wenzel.
Peter Heina, General Manager of Wenzel Steintechnik, if the Great-Great Grandson of the original stone carver, and has kept the family business moving forward and growing with the times. Currently, Wenzel Steintechnik is responsible for bringing the raw material in from the quarry, and processing it to rough size for our factory.
Work begins typically with a 35 ton block of raw material which is sawn into workable sizes for either machine tables, or components such as X beams. These smaller blocks are then moved to other machines for finishing to their final sizes. This may seem like no big deal, but having seen it in person, I have a new appreciation for the task. Working with such massive pieces, while also trying to maintain high precision and quality, is a balance of brute force and a delicate touch that requires a level of skill and passion to master.
This skill and passion extends outside of the Steintechnik facility though. Each year Peter makes
regular visits to the South African quarry where our granite is sourced, not only to maintain a good relationship with our vendor, but also to collaborate on selecting the individual blocks which will become Wenzel CMMs. In 2003,
Peter led a project at the quarry to improve their processes for handling the massive stones, in order to improve the quality and yield of the finished product which we receive at Wenzel Steintechnik. This allows us to make more, and larger pieces from a single block of stone, improving our lead time and efficiency.
This spirit of continuous improvement carries on at our Steinechnik facility as well. Recently Wenzel has invested in a new 5 Axis vertical mill, to streamline the manufacturing process, and reduce the handling of the stone. This massive gantry mill allows Peter and his team to combine cutting, grinding, and milling operations into one, while also improving the cycle time of the processes themselves, which led to a 60% reduction in overall processing time.
With a working volume that can handle up to 6 large machine bases, Wenzel Steintechnik now has the capability for lights out production of granite, 24/7. Improvements like these allow us to reduce our delivery times to the end customer, and also increase the flexibility of our production schedule to react faster to changing demands.
Another more subtle change in the manufacturing process, happened some years ago, when the Steintechnik team began serializing all the components they manufacture. This allows them complete traceability form the time a block of raw granite leaves the quarry, until the pieces are assembled into a CMM.
Should problems arise with a certain component, all other components which could be affected can be easily contained and verified for their quality, ensuring that no quality defects escape the facility.
This may be something we take for granted in high volume production like Automotive and Aerospace, but it is unprecedented in the world of granite manufacturing.
But there’s more to the quality of our granite than just the size and shape. What about the mechanical properties? How do we ensure that the physical quality and the composition is what we expect? The technicians at the factory perform a variety of tests; they check the composition, perform physical tests, even grind and lap samples to ensure that the necessary flatness and durability can be achieved.
But when the giant monoliths are first received in Steintechnik, Peter Heina performs his own test, with water. Cutting a small sample from the block, Peter runs water over the stone, feeling it with his fingers. The way the block slides in his hands, how it absorbs or repels the water, whether bubbles form on the surface.
These are all indicators of how the block will perform during grinding and lapping, whether micro-fissures exist that will cause cracking and deformation. In essence, is it good enough for a Wenzel?
So why, you may ask, does this all matter? Why should you care about our granite? The fact is if we’ve done our job right, you never need to. The level of care we take to ensure that only the best material is used in the construction of our machines is a core principle, the center of all we do.
We build our machines on a 130 year old tradition of quality and care that ensures the highest level of precision, and durability. We take the time to use the best materials, and the best processes, building an accurate and stable machine so that you don’t have to think about it. Anything less, wouldn’t be a Wenzel.