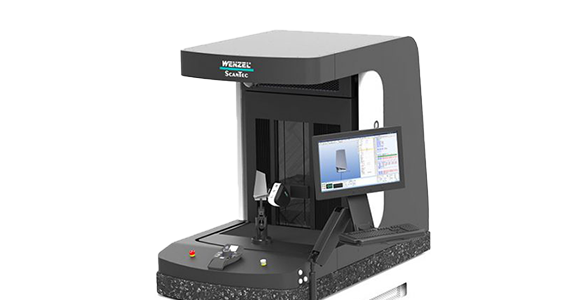
Gas turbine propulsion systems are extensively used in aerospace and defense, as they are a key element of aircraft engines and even marine warships. Due to the precision required to build and properly assemble a gas turbine, CMMs (coordinate measuring machines) are frequently used during the production process.
In this article, we’re going to explore the impact and importance of gas turbine testing, the challenges many aerospace and defense manufacturers face when building and measuring these turbines, and how your organization can significantly improve production and quality control processes by using precision CMMs produced by WENZEL.
Impact & Importance of Testing
Gas turbine blades require an incredible amount of precision and tight tolerances in the manufacturing process; this is to ensure a long lifecycle and prevent premature wear and tear due to operational stresses and strains.
Because of these strict tolerance requirements, inspections are performed with CMMs during the quality control and quality assurance (QA) phase. In CMM inspections, each blade is quickly measured in order to identify whether or not it meets specifications.
By using a multisensor CMM, a turbine manufacturer can rapidly measure the complex geometry of a turbine blade in one single set-up, without having to rotate the blade on various axes or use additional mathematics and transformations in order to align multiple coordinate systems.
CMMs are also used to measure stresses and strains during testing and to identify any deformation. If any deformation is found, the turbine blades in question must be either repaired or replaced before they are shipped off to the final stage of the production process.
Challenges
Because turbine blades have complex geometry, angles, curvature, and tight spaces, measuring them can be a challenge that most conventional measuring instruments can’t handle.
Fortunately, multisensor CMMs solve this problem by combining tactile sensors, optical and vision sensors, chromatic white light sensors, and surface scanning data all into one singular model. By using multiple sensors to get as much information on the part as possible, these CMMs are able to measure each turbine blade with a greatly enhanced level of accuracy compared to competing measurement methods.
If your organization has been struggling with quality control, using an advanced CMM, like WENZEL’s CORE D model, will allow you to finally measure each turbine blade in a single setup without any extra hassle
Learn More From WENZEL Today
WENZEL is a family-owned business and leading manufacturer of aerospace metrology solutions. There are over 10,000 WENZEL measurement machines installed in over 50 different countries to date, and the WENZEL brand is known throughout the industry for its reliability and precision.
If you have questions about inspecting gas turbine blades with CMMs, or want to learn more about our CORE D product, please contact one of our specialists today.