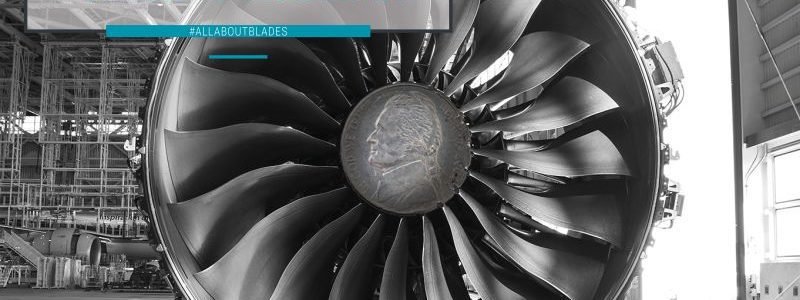
Why using nickel makes sense for turbine blades
The story of modern turbine blades has usually focused on the shape for me. There are good ways to measure turbine blades and even better ways to measure turbine blades.
The focus of this article will be on the material side vs. the shape. The star of the show is the humble element, Nickel.
The majority of what I found on this subject is here. The Superalloys Fundamentals and Applications by Roger C. Reed. This book will give you a thorough understanding of nickel alloys.
Nickel alloys allow the higher temperature ranges required by modern jet engines.
An additional requirement is single-crystal (SX) super alloys make up the blade as well.
In the table below, the composition by weight of the alloys are given. Some of the common alloys used. Some alloys have over 10 various elements in them.
More information on SX Turbine blades
Once you have the material the investment cast process, specifically the Bridgeman process, is used to fabricate the blades. From “On the Fabrication of Metallic Single Crystal Turbine Blades with a Commentary on Repair via Additive Manufacturing”
The blades are then heat treated. From that referenced article above.
“The ceramic topcoat is responsible for thermally insulating the blade and is generally composed of yttrium oxide (Y2O3)-stabilized zirconium oxide (ZrO2) or YSZ. YSZ displays a wide range of advantageous characteristics making it a favorable material for the topcoat. When compared to all other ceramics, YSZ displays one of the lowest thermal conductivities at high temperatures.”
Four main conclusions from “On the Fabrication of Metallic Single Crystal Turbine Blades with a Commentary on Repair via Additive Manufacturing” are as follows: Materials, Manufacturing via Investment Casting, Repair via Additive Manufacturing, and On the Fabrication of Metallic Single Crystal Turbine Blades with a Commentary on Repair via Additive Manufacturing. I cannot over emphasize reviewing the article . It will give you a better understanding of how modern turbine blades are made and the challenges.
Nickel – “I hardly knew ye”
As mentioned in the previous #allaboutblade blogs the first engines were made of steel and had serious short comings. They just did not have the temperature capabilities to go above 500C and in next week’s blog we will look at the history of how these blades sit in around 1800C which is above the melting temperature of the blade it self and operate optimally. This is where our hero comes into play and not only save the day but change the economics of aviation, blade innovation and air travel.
I have to mention how special nickel is. I took it for granted. Doing some of the material research I found Nickel’s own fan site, with a great About Nickel page from the https://nickelinstitute.org/.
Nickel stats for the curious – Wikipedia source
Join our innovation journey by following WENZEL’s LinkedIn page where we share all the latest metrology news as well as interesting product information that you don’t want to miss. Best of all is our Metrology Mondays, Tuesday Tech Tip Videos and #allaboutblades blogs on Wednesdays.
Metrology Monday
https://www.youtube.com/watch?v=R-IbJQ0VEuwhttps://www.youtube.com/watch?v=n67_u-dfKYM